Current Issues Faced by Miners with Caterpillar Bushings
Created from bronze with a small diameter flanged thrust face, the OEM’s bushings structure can be insufficient for the loading conditions in certain environments, resulting in accelerated wear on the thrust face, and posing concerns for durability and longevity.
The solution offered by the OEM was adding a thrust ring to the bush flange's outer diameter. The attempted fix did not yield the desired results, leaving the mining companies grappling with ongoing wear and maintenance issues. Additionally, the lack of seals in the standard arrangement exposed the bushings to contaminants and abrasive materials, exacerbating the wear rate and decreasing the longevity of the components.
Leveraging Our Solutions for Increased Asset Life Within Caterpillar 6020B Excavators
We understood the challenge and immediately started exploring alternatives to enhance the specifications to create a longer-lasting alternative. This led our metallurgic team to review a solution we designed in 2010 to solve the issues related to the thrust plate failures of Hitachi excavators – the Geographe EP Top Hat Bush.
Leveraging the success behind creating the Geographe Enhanced Performance™ (EP) Top Hat Bush for the Hitachi Excavator, we upgraded the standard bronze bushes to case-hardened steel to suit Caterpillar 6020B excavators and by incorporating a larger thrust face for improved contact surface area.
The Geographe EP Top Hat Bush is also sealed with a split seal at the thrust face which can be changed out without disassembly, allowing for optimal bush performance, solving premature wear challenges and resulting in reduced downtime and increased productivity.
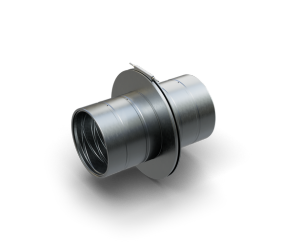
Improvement Factors of the Geographe Enhanced Performance™ Top Hat Bush
- Retrofittable, allowing for compatibility with standard bore diameters.
- Case-hardened steel for increased durability.
- Cross-hatching to provide superior lubrication.
- Larger flange diameter for a greater thrust surface area.
- Incorporated seal in the bush bore to retain grease in the work zone.
Benefits of the EP Top Hat Bush to the Caterpillar 6020B Excavator Fleet
- Increased ease of fitment, reducing maintenance times and associated labour costs.
- No hot work is required, eliminating high-risk work and reducing machine downtime associated with gouging, welding, and line boring.
- Manufactured from one piece of material, the part is significantly stronger and not prone to movement under dynamic load conditions.
- Incorporated flange OD split O-Ring for contaminant exclusion and grease retention.