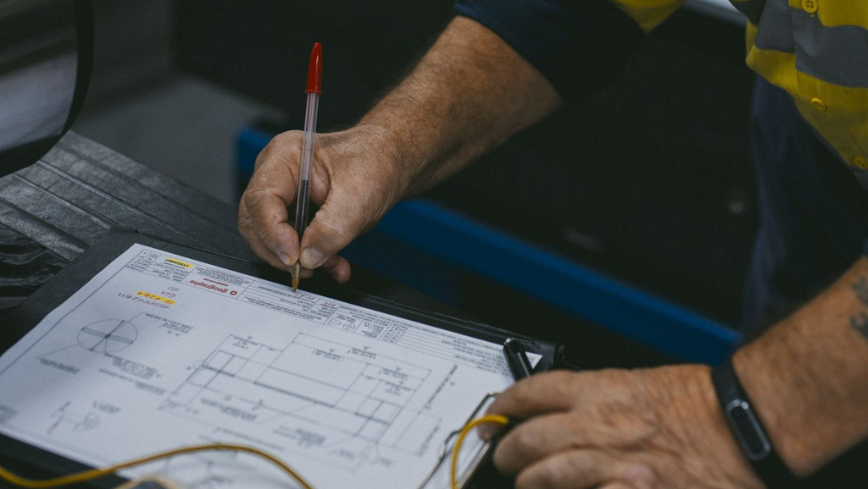
When you have eliminated the impossible, whatever remains, however improbable, must be the truth… Sherlock Holmes -The Sign of the Four (1890)
Failure analysis is an investigative process whereby data is collected and analysed to determine the cause of failure. In an industrial setting such as the mining industry, failure of a component can snowball into wide ranging consequences from: downtime to loss of production, throwing maintenance and labour schedules into disarray as well as, in some cases, cause safety issues. Making the decision to have those components analysed for cause of failure can either reassure you or trigger some important changes. So, here are some reasons why we love failure analysis – and you should too!
Become a Detective
Being a failure analysis expert allows you to become the “Sherlock Holmes” in a mystery novel. The tools may be different – a spectrograph to inspect materials closely or hardness tester… but the ‘cool’ factor is the same. You are the analyst ultimately responsible for investigating how a component or piece of fixed plant like a gearbox has come to its demise. Gross mishandling? Unfit materials? On the other side of the coin, as the responsible person who initiates the investigation, you too become invested in that process and can disseminate the findings to the appropriate personnel.
Treat the Cause, Not the Symptom
There is nothing more satisfying to know that by getting to the root cause of a problem you have the opportunity of preventing that problem from occuring again or alternatively delaying it if it is unavoidable. In most cases, a simple engineered design solution is all that is needed to fix a component that is repeatedly failing prematurely. Alternatively, a different maintenance practice can often be advised to avoid failure. Isn’t that great knowledge?
Be abreast of Enhanced Performance Solutions for Mining Parts
Know what is at Fault
If your crew is not handling products correctly or the products themselves are inherently faulty – wouldn’t you rather know? As a maintenance manager, it is your duty of care to look after your fixed plant or fleet’s continued performance. Failure analysis can provide those answers and either put you at ease knowing who could possibly be at fault – the end user, or the manufacturer. It can sometimes be the case that no one is at fault, however, the product has originally been designed to not be as fit for purpose as required in exceptional operating conditions. That is also good knowledge to have.
Delivering Best Practice
Once failure analysis results are in, this is your chance to don the superman cape and get onto implementing change or preventative measures. You can be part of the change that creates greater performance results.
How can we help?
Submit your details below and our team will contact you.
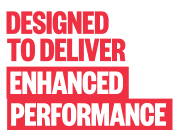