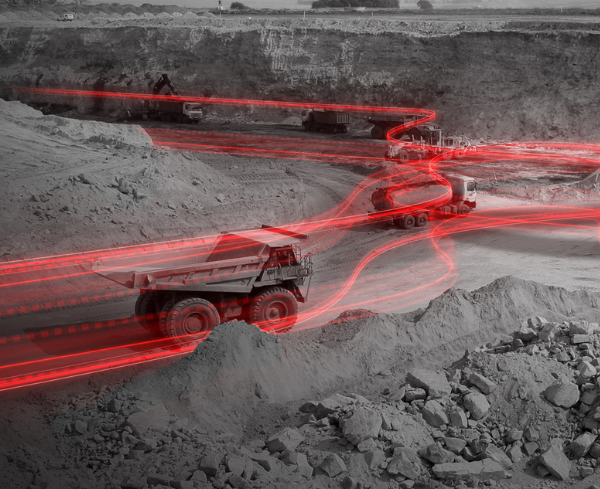
In a time where mining companies must balance being cost-conscious with increasing fleet uptime, looking for parts that add value and drive down costs is more important than ever.
It’s no secret that times are tough in the mining industry at the moment.
Navigating around new and emerging macroeconomic and microeconomic factors, mining companies are increasingly seeking ways to source high-quality parts that are cost-effective and delivered on time. Understanding this, Geographe comes up with a solution to this challenge.
“In the industry, customers are looking for reliable wear parts that sites can confidently fit in earthmoving equipment to achieve output goals, that also don’t cost a substantial amount” said Geographe Chief Customer Officer Roy Chowdhry.
“We have significant replacement wear part kits, and enhanced performance offerings that suit major heavy earthmoving equipment such as haul trucks, excavators and ancillary machinery.”
On top of the challenge of being cost-conscious, mine sites can often find it difficult to find aftermarket products that are specific to a site’s unique environment and needs.
Luckily enough, Geographe has already planned for this.
“We work with every Tier 1 miner on the ASX (Australian Stock Exchange), and actively service over 100 mine sites across Australia and work with a further 300-plus customers both nationally and internationally,” Chowdhry said.
“Their concerns are often similar when it comes to aftermarket parts. They want the parts fit for purpose, of OEM (original equipment manufacturer) equivalent quality or higher, have consistent supply and availability and come with an industry-standard warranty."
“What we actively do is invite customers who wish to see where their parts are made and get them to see from an end-to-end perspective how it is done. Customers usually leave impressed with how much knowledge, technology and automation exists in regional Western Australia.”
Geographe also offers parts kits for various machinery, ensuring that replacement kits meet mining operations' specific cost and performance needs.
“Our team develops and customises parts kits, based on a miner’s specific requirements,” Chowdhry said. “This can be a full rebuild kit, or just a kit based on the parts they know wear most frequently.
“Taking this flexible approach allows us to supply only what our customers really need. These bespoke kits are built into the job scope. They help avoid waste at a site level and cost at a corporate level.
“We implement robotics and automation via our sales and operational planning processes to optimise costs and engineer products through lean processes. This allows us to produce a very high-quality product made in Australia at competitive prices.”
Chowdhry highlighted the Ball Stud Kits Geographe manufactures to suit Caterpillar 7-series haul trucks.
“They have a very strong reputation in the market for longevity and safety which is what is required for critical steering components,” he said.
“With thousands sold and zero reported fleet breakdowns, the Geographe ball stud kits keep trucks running for longer and can come up to four times oversized to help keep costs down in the mating steering components.
“Even those these ball studs have been enhanced by Geographe, they’re still a lower cost alternative than the OEM.”
Above all, Geographe ensures it maintains strong relationships with its mining customers to help them get the reliable replacement wear parts they need.
According to Chowdhry, that starts with listening closely to what the customer is after.
“If we’ve already identified a core problem and developed a solution, we can share how it’s already helped others and how it may be the right fit,” he said.
“If not, we can partner with them to develop a new idea. We hold regular meetings both with maintenance and reliability teams on-site, and with corporate counterparts at their offices.
“Quarterly, we work to report on contract utilisation to help ensure that companies get the most from their agreement with Geographe.”
Importantly, Geographe works to ensure any customer problems are solved quickly to ensure minimal downtime on-site.
“We try hard to maintain close customer relationships and try and identify any pain points they have in their machine fleet before they become major issues,” Chowdhry said.
“Understanding that mine sites are more cost-conscious than ever means we will continue to collaborate closely with customers to offer high-quality parts that support fleet up-time while driving down maintenance, repair and operation costs.”
Featured in Australian Mining, October 2024 edition: https://www.australianmining.com.au/navigating-the-need-for-cost-conscious-componentry/
Be abreast of Enhanced Performance Solutions for Mining Parts
How can we help?
Submit your details below and our team will contact you.
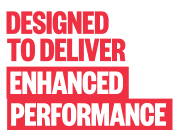