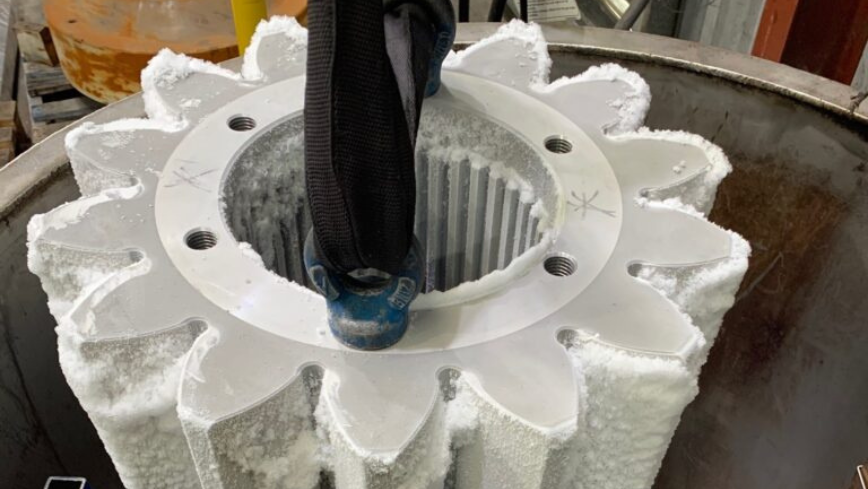
The advanced process of Deep Cryogenic Treatment involves bringing the temperature of components down to temperatures below -180⁰C in a controlled manner.
Cryogenic Processing alters the crystalline structure, transforming it into a more uniform and durable construct.
These changes become permanent as the temperature of the material is gradually brought back up to room temperature or beyond.
The Deep Cryogenic Treatment process:
Liquid nitrogen is passed through a ‘liquid to gas’ heat exchanger used in conjunction with a circulating fan.
The heat exchanger contains the boiling liquid nitrogen and absorbs the thermal shock, while the fan circulates gaseous nitrogen over the heat exchanger and the payload to slowly remove the payload’s latent heat. The loss of energy to the external environment is minimal due to the vacuum insulated Dewar.
The payload is slowly ramped down from ambient temperature to -184⁰C over 7 hours, held at temperature for approximately 20 hours before returning to ambient temperature. The payload is then transferred to a furnace for tempering at 180⁰C for several hours.
"DCT improves the quality, durability and lifespan of a range of industrial machine parts that are susceptible to wear due to stress, friction and fatigue."
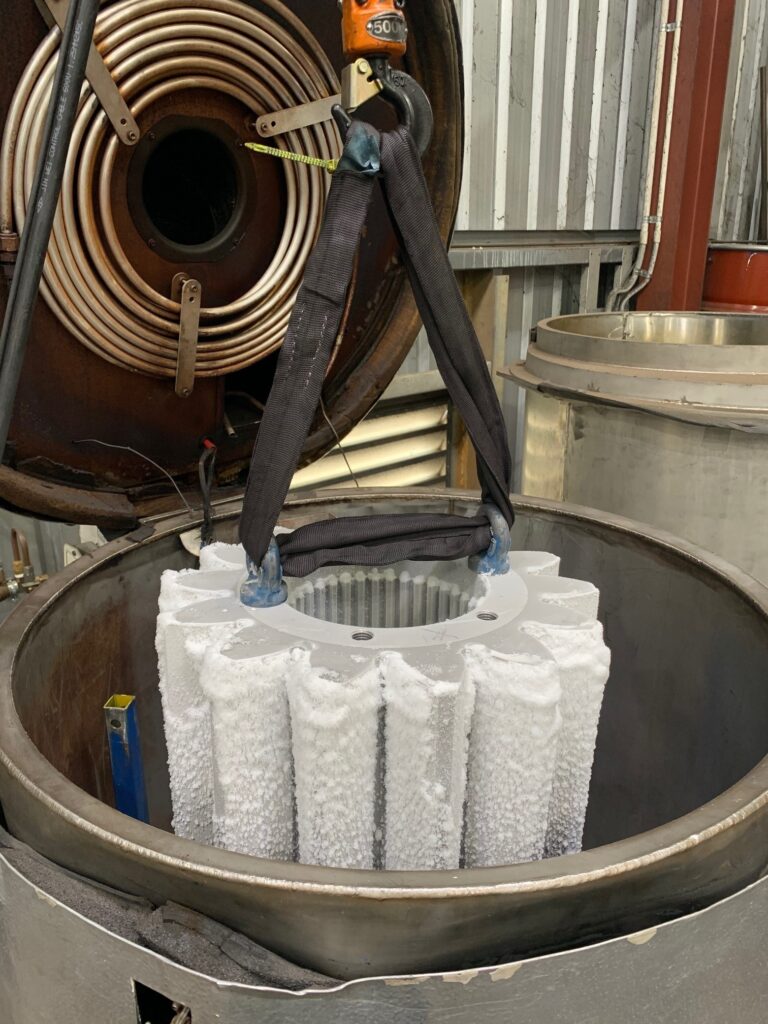
Benefits of Deep Cryogenic Treatment include:
1. Increased hardness and hardness consistency through transformation of retained austenite to martensite.
2. Improvements in fatigue and wear resistance.
3. Reduced internal stress leading to improved dimensional stability.
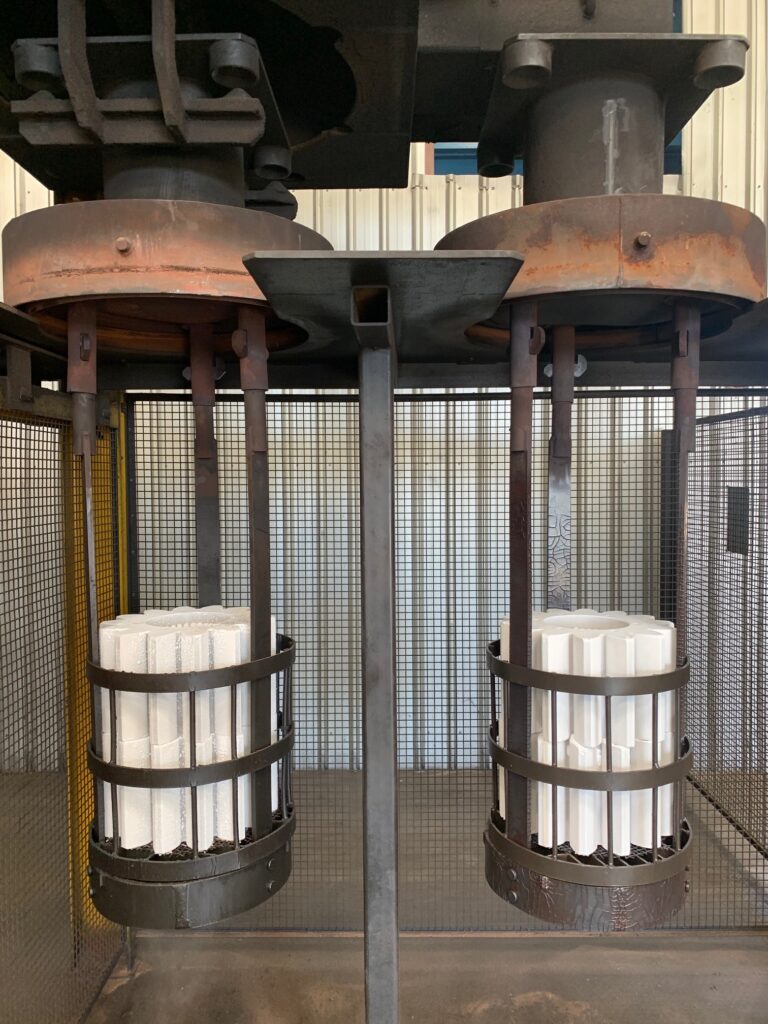
Be abreast of Enhanced Performance Solutions for Mining Parts
How can we help?
Submit your details below and our team will contact you.
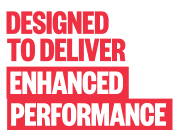